KNOWLEDGE CENTER
What is Thermoplastic Elastomer (TPE)?
Thermoplastic elastomers (TPEs) are a versatile class of materials that combine the flexibility of rubber with the easy processing of plastics. Unlike traditional rubber, TPEs can be melted, molded, and reshaped like plastics, making them more efficient and cost-effective for manufacturers. Their unique composition consists of both a hard plastic phase and a soft elastomer phase, allowing them to stretch and bounce back like rubber while also offering the processing benefits of thermoplastics. This dual advantage has made TPEs increasingly popular across industries such as automotive, footwear, healthcare, and consumer goods. The ability to provide both durability and flexibility, while being recyclable and more sustainable than traditional rubbers, has cemented TPE's place as a go-to material in modern manufacturing. So, what exactly is driving the rising demand for TPE in various industries today?

Key characteristics of TPE include:
Flexibility: Similar to traditional elastomers, TPEs are highly flexible and can stretch significantly.
Recyclability: Unlike vulcanized rubbers, TPEs can be reprocessed and recycled, reducing environmental waste.
Durability: TPEs are highly durable, offering excellent resistance to wear, abrasion, and chemicals.
Cost-effectiveness: They can be easily molded into various shapes, making them an economical choice for mass production.
Types of TPEs
There are several types of thermoplastic elastomers, each designed to meet specific application needs. Some of the most commonly used TPE types include:
Styrenic Block Copolymers (SBC): Known for their excellent clarity, flexibility, and ease of processing, SBCs are widely used in packaging and medical applications.
Thermoplastic Polyurethanes (TPU): TPU offers high mechanical strength and is often used in footwear, automotive parts, and electronics.
Thermoplastic Vulcanizates (TPV): TPVs combine the best of rubber and plastic properties, making them ideal for automotive seals, hoses, and weatherproofing.
Copolyester Elastomers (COPE): These TPEs are known for their resistance to heat and chemicals, making them suitable for industrial applications.
Polyether Block Amides (PEBA): PEBA materials are lightweight and have excellent low-temperature performance, often used in sports equipment and medical devices.
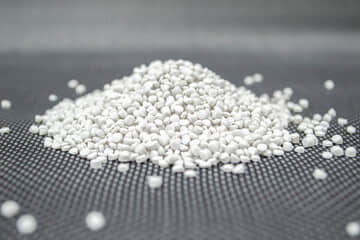
what are the applications of thermoplastic elastomers
Thanks to their unique properties, thermoplastic elastomers are used in a wide range of industries. Here are some of the key application areas:
Automotive: TPEs are extensively used in the automotive industry for manufacturing seals, gaskets, interior parts, and cables due to their resistance to heat, oil, and abrasion. TPVs, in particular, are popular for their durability and flexibility in producing car components.
Footwear: TPE compounds are widely utilized in shoe soles, offering a combination of comfort, flexibility, and durability. Thermoplastic polyurethanes (TPUs) are often preferred for midsoles, while softer TPEs are used for slippers and casual footwear.
Medical Devices: TPEs are commonly used in medical tubing, gaskets, and seals. Their biocompatibility, flexibility, and ease of sterilization make them ideal for healthcare applications. SEBS-based TPE compounds are particularly favored due to their stability in medical environments.
Consumer Goods: From toothbrushes and power tools to razors and grips, TPE materials are present in various household items. Their excellent overmolding capabilities allow manufacturers to enhance grip, comfort, and functionality.
Construction: In the construction sector, TPE materials are often used in weatherproofing seals, window profiles, and industrial mats. Their resistance to UV exposure and harsh weather conditions makes them ideal for outdoor applications.
Advantages of Using TPE Materials
Thermoplastic elastomers offer a wide range of benefits that make them stand out as a material of choice in numerous applications:
Sustainability: One of the most significant advantages of TPEs is their recyclability. Unlike traditional rubber, TPE materials can be melted down and reused, making them an eco-friendly option.
Cost-Efficient Processing: TPEs can be processed using standard plastic manufacturing techniques like injection molding and extrusion, reducing production time and costs.
Versatility: Their ability to be molded into complex shapes and overmolded onto other materials enhances design flexibility for manufacturers.
Enhanced Performance: TPEs offer excellent resistance to chemicals, UV light, and temperature fluctuations, making them suitable for demanding environments.
Customizability: TPEs can be engineered to meet specific performance criteria, such as hardness, color, and elasticity, allowing manufacturers to create tailored solutions for various applications.
Challenges and Limitations of TPE
While TPE offers numerous advantages, it is not without its challenges:
Temperature Sensitivity: While TPEs are more resistant to heat than traditional rubbers, they may not perform as well in extreme high-temperature environments compared to thermoset elastomers.
Cost: Some TPE grades, particularly those with enhanced properties, can be more expensive than conventional rubbers or plastics.
Mechanical Strength: TPEs may not always match the mechanical strength of vulcanized rubber in some high-stress applications.
The Future of Thermoplastic Elastomers
As industries increasingly focus on sustainability, recyclability, and performance, TPEs are expected to grow in popularity. Innovations in TPE formulations are likely to enhance their mechanical properties, making them suitable for even more demanding applications, from aerospace to advanced medical devices.

Why TPE is the Material of the Future
Thermoplastic elastomers are revolutionizing industries with their blend of rubber-like flexibility and plastic-like processability. Their sustainable, cost-effective, and versatile nature makes them an excellent choice for manufacturers looking to innovate in fields ranging from automotive to healthcare.
With ongoing advancements in TPE technologies, these materials are set to play an even more significant role in the future of manufacturing, offering endless possibilities for product development and innovation.